-
Notifications
You must be signed in to change notification settings - Fork 3
Dendrometer Updates
Dendrometer Updates | Main Page
Author: Nicholas Le
Show More
During the Summer 2023 growing season from approximately May to October, we deployed dendrometer devices on multiple different types of plants at different locations.- 32 dendrometers were installed on grape plants at Southern Oregon Research and Extension Center (SOREC).
- 15 dendrometers were installed on blueberry plants at Lewis-Brown Farm.
- 6 dendrometers were installed on hazelnut plants at North Willamette Research and Extension Center (NWREC)
Teros 10 Soil moisture probes were used with the dendrometer for the first time at LB and NWREC.
Author: Cameron Clonch
Show More
On April 30th, 2022, we visited the Southern Oregon Research and Extension Center (SOREC) for our first deployment. We installed 12 devices at DANCIN Vineyards in collaboration with out stakeholder, Dr. Alexander Levin. Each plant has two dendrometers; we installed on plots receiving two different water treatments. Each device is operating with 4G telemetry capabilities; 5 - 6 times daily, a data packet from each node is sent to a central hub (deployed in the vineyard and being powered via a solar panel) and is then transmitted to the research station a few miles away. The devices will be running for the duration of the growing season (May - September). We intend to do a second deployment consisting of 20 dendrometers (for a total of 32) in the beginning of June - and will use the same installation strategy of 2 devices per plant.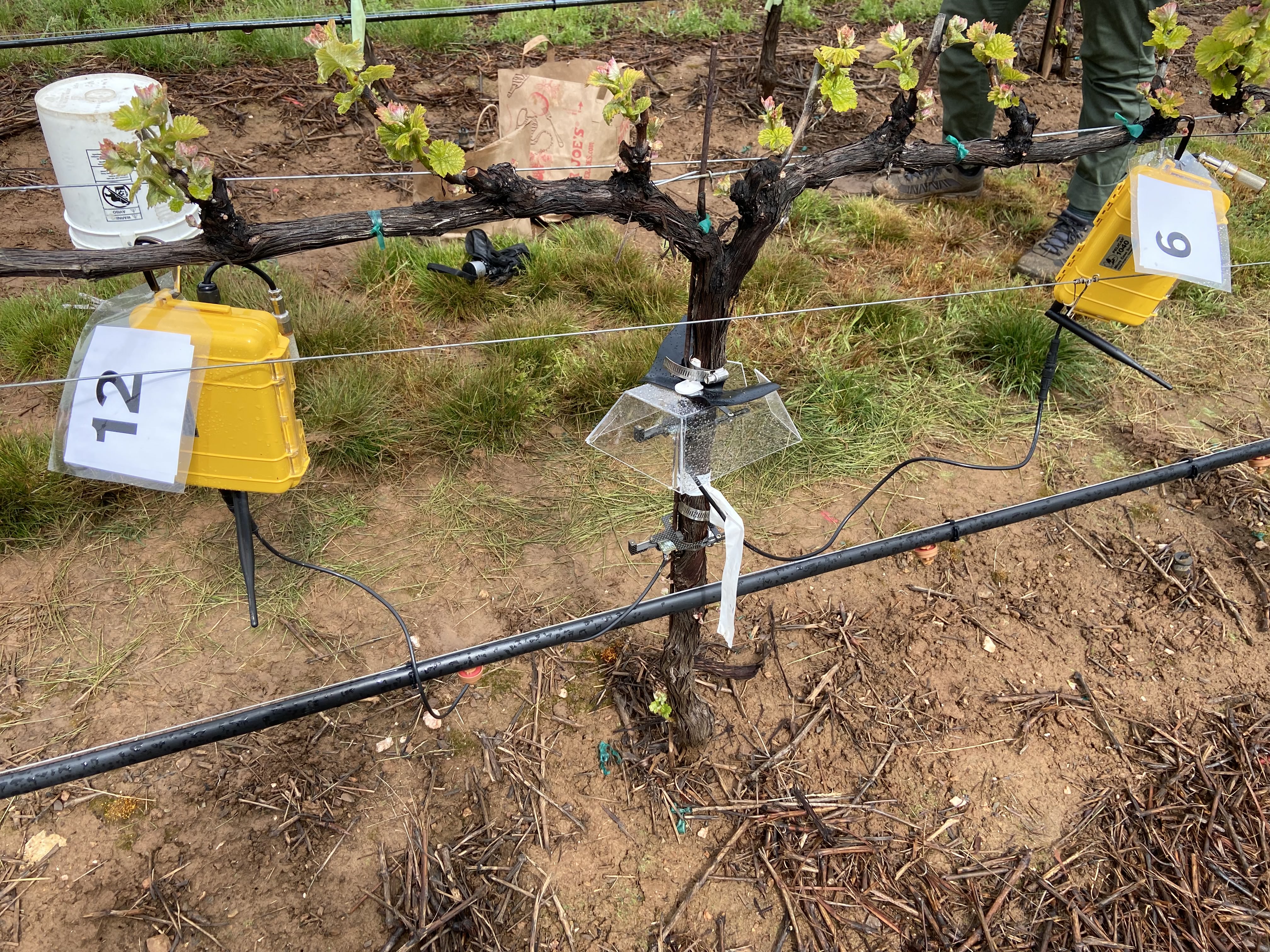
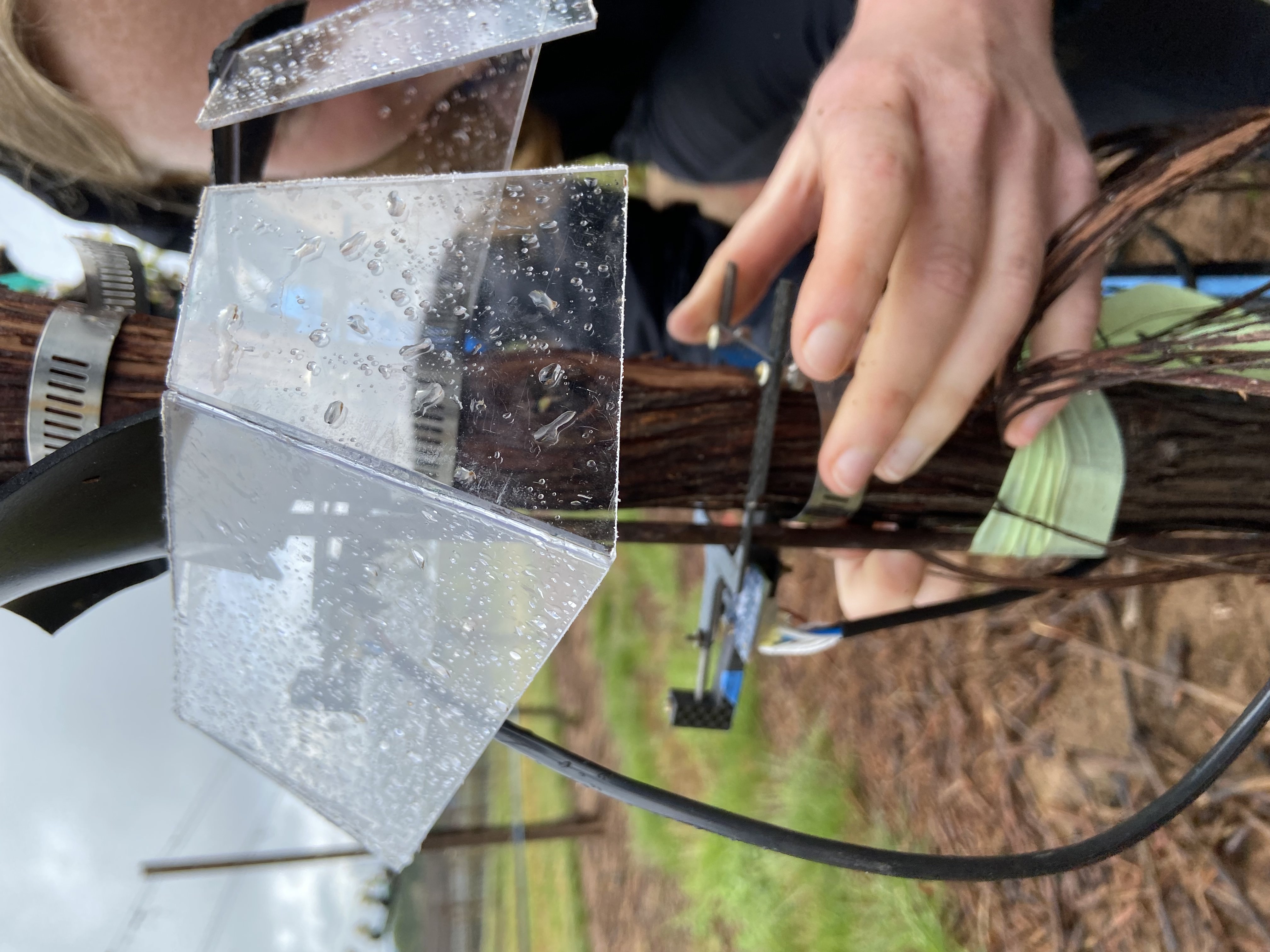
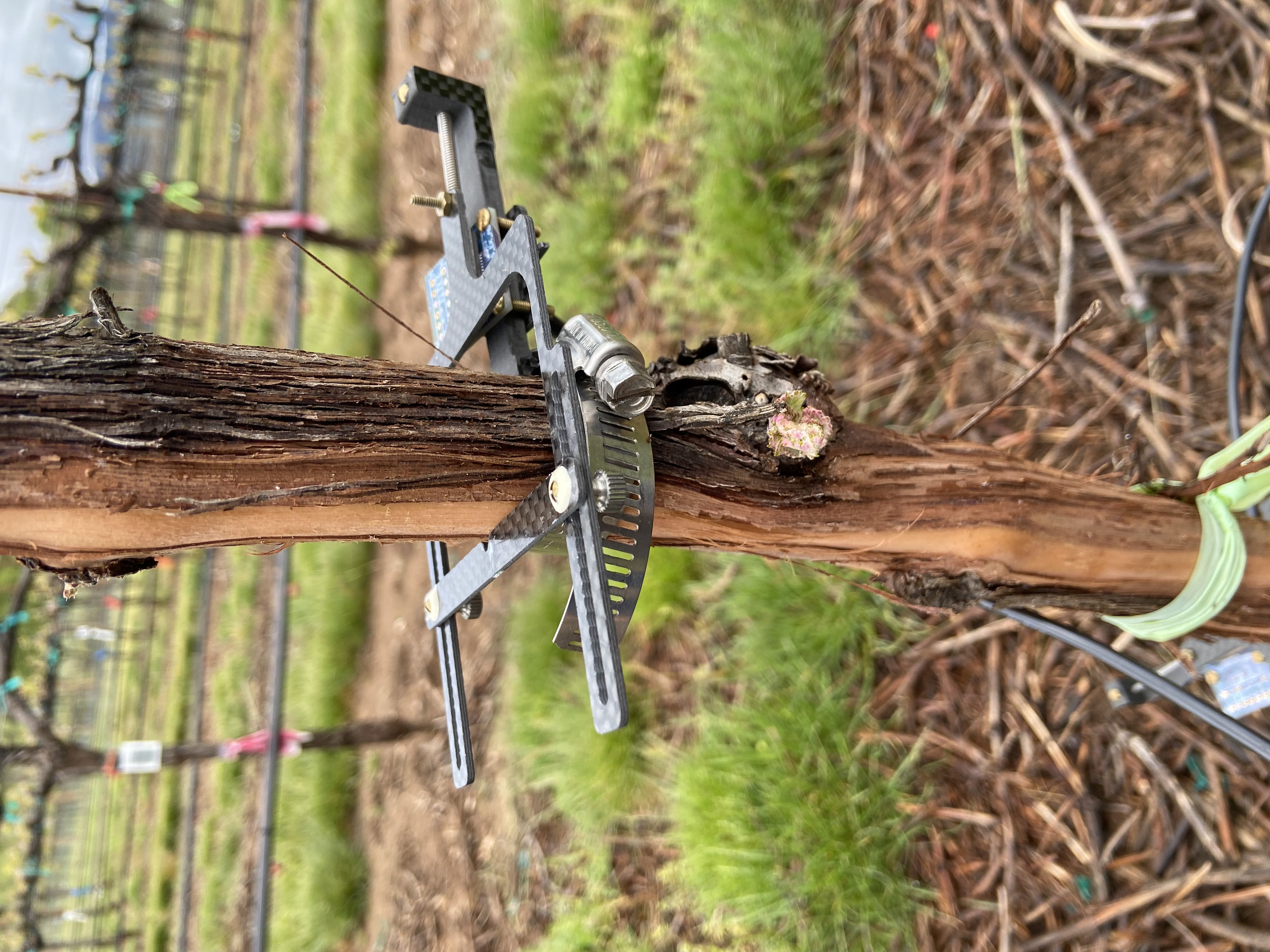
Author: Bryson Goto
Show More
Collaborating with both the Lewis-Brown farm and the Southern Oregon Research and Extension Center (SOREC), the Dendrometer team have deployed 21 dendrometer units to measure diurnal fluctuations for blueberry plants as a validation test for our later deployment on grapevines. This field test will reveal any remaining bugs in the code to fix before our summer SOREC deployment as well as provide data for the Lewis-Brown farm about the status of their blueberry plants.Author: Henry McCreery
Show More
In the past months, we have manufactured parts for the 12 new dendrometers and refurbished the electronics of the 20 original dendrometers. The maximum diameter the dendrometers need to accommodate has been increased from 40 to 55mm, so new slider parts are being manufactured to meet that requirement. 3d printed case inserts have been designed and manufactured in order to hold the node electronics when the case is in an upright position. We will be doing two deployments, one in the sprint and one at the beginning of the summer, and the spring deployment dendrometers will need to survive the more intense sprays and rains during that time. As such, a weatherproofing system has been designed and prototypes manufactured. In order to extend the life of the batteries in the field, the code has been altered so that live updates are transmitted much less frequently (data is still stored locally at the original ~15 minute interval).Author: Bryson Goto
Show More
After meeting with our stakeholder Dr. Levin, we have decided to continue with the dendrometer deployment in the summer of 2022 in the SOREC vineyard. We have learned a lot from this previous deployment from the data as well as the dendrometer making and deploying process that will help us with a better deployment. This summer we'll be deploying 32 dendrometer nodes with 1 central LoRa hub that will be installed to upload each node's data through a 4G network. This node will be charged with a solar panel throughout the day to ensure it will last in the field when connecting to the internet.We look forward to continue working with Dr. Levin in the SOREC deployment and hope we both gain a lot from this experience.
Author: Cameron Clonch
Show More
Winter Testing
To further test/validate the dendrometer, we are performing several experiments during the off-season using the devices from the summer SOREC deployment. For on-plant tests, we have acquired an orange tree and greenhouse space. We are also continuing to collect data from blueberry plants at Lewis-Brown farm. Some examples of experiments we will carry out are: installing each dendrometer on a Pyrex cylinder (known for its extremely small thermal expansion coefficient) to verify temperature independence and evaluate drift; putting the dendrometer on a pipe and running water (at various temperatures) through the pipe; and installing several dendrometers on the same plant to test redundancy. These are just a few examples of the experiments we hope to conduct. Each experiment will take place for at least two weeks.
Thus far, eight dendrometers have undergone Pyrex testing for at least two weeks. A few of the dendrometers show a drift of about 10 microns, while others have only recorded fluctuations of +/-0.5um (and remain centered at zero relative displacement). We will continue to test to evaluate this observed drift, as well as occasional random jumps in the data. The two dendrometers installed on the orange tree have shown average daily diameter fluctuations of 50-60um; the data from each device closely match one another.
Design Updates
On top of validation efforts, the dendrometer design will be updated with additional protection mechanisms to avoid interference from wind, rain, and other weather-related events. Namely, a protective cover is being designed. The cover will be separate from the device itself, but attach to the vine in a similar manner.
The electronics are being updated to have 4G capabilities and improved LoRa communication. The new version of the dendrometer will also have an updated PCB.
Publications
The HardwareX paper for the dendrometer project has officially been published. It can be found here.
We are also in the process of pursuing several design patents.
Author: Cameron Clonch
Show More
SOREC Deployment with Dr. Alexander Levin
The bulk of the data from our deployment at the Southern Oregon Research and Extension Center (SOREC) with Dr. Levin has been collected. The SOREC deployment involved plants undergoing two different water treatments. Dendrometers were placed on ten different plots (there are typically 6-8 plants per plot); two dendrometers within each plot (although a couple plots only had one dendrometer due to limited supplies). Five of the plots received one water treatment, while the other five plots were on a different irrigation schedule. It is expected that the data trends from dendrometers within the same plot will be the most similar.
Despite some battery issues, we were able to collect data (displacement, temperature, humidity) on most devices from July 1st to mid-August. Of the seventeen deployed dendrometers, sixteen successfully tracked daily fluctuations in trunk diameter. However, the data still contains some noise and there are periods of time within the overall deployment range in which some devices were not collecting usable data. It is believed that some of these issues were due to interference from vineyard maintenance as the dendrometers were only able to be checked on once every 1-2 weeks. The results further prove a need for an improved form of shelter for the dendrometer mechanical body and value of telemetry capabilities. Further analysis is currently being conducted by our OPEnS dendrometer team and Dr. Levin.
Lewis-Brown Deployment with Dr. Maria Zamora Re
2/3 dendrometers have continued to successfully transmit data using LoRa telemetry. There are some gaps in the data acquired with telemetry, which are theorized to have been caused by weather interference. Despite the dysfunctional telemetry on the third dendrometer; we confirmed that it has been logging data to SD; just the telemetry element is not working. The devices were moved on 9/30 to different plants and the LoRa hub was relocated to a more open spot that will hopefully improve data transmission rates / telemetry functionality.
Author: Bryson Goto
Show More
Another stakeholder of ours, Maria Zamora Re, requested us for 3 dendrometers to be used for testing in the Lewis-Brown farm on blueberry plants. We deployed last week with 3 dendrometers as well as a LoRa hub connected to Ethernet for telemetry to upload the data to a Google Sheets page. 2/3 dendrometers consistently upload to the Google Sheets page while the last dendrometer hasn't connected thus far. This is the first time we're testing our telemetry in a deployment and we'll be sure to improve the design for better results.
Author: Bryson Goto
Show More
Cameron and I went to SOREC for the second part of Dr. Alexander Levin's deployment where we deployed 8 more dendrometers into the vineyard, checked up on the previous 10 dendrometers, collected the saved data, and uploaded new code onto the first set of deployed dendrometers. The code was uploaded for minor fixes and enhancements.
Out of the 10 previously deployed ones, 8 were still functioning as intended. 1 had battery issues and 1 was taken back for repair. Below shows one of the graphs that was collected from the vineyard. It graphs the displacement (vine shrinkage / growth) in relation to the vapor pressure deficit (VPD) at the time.
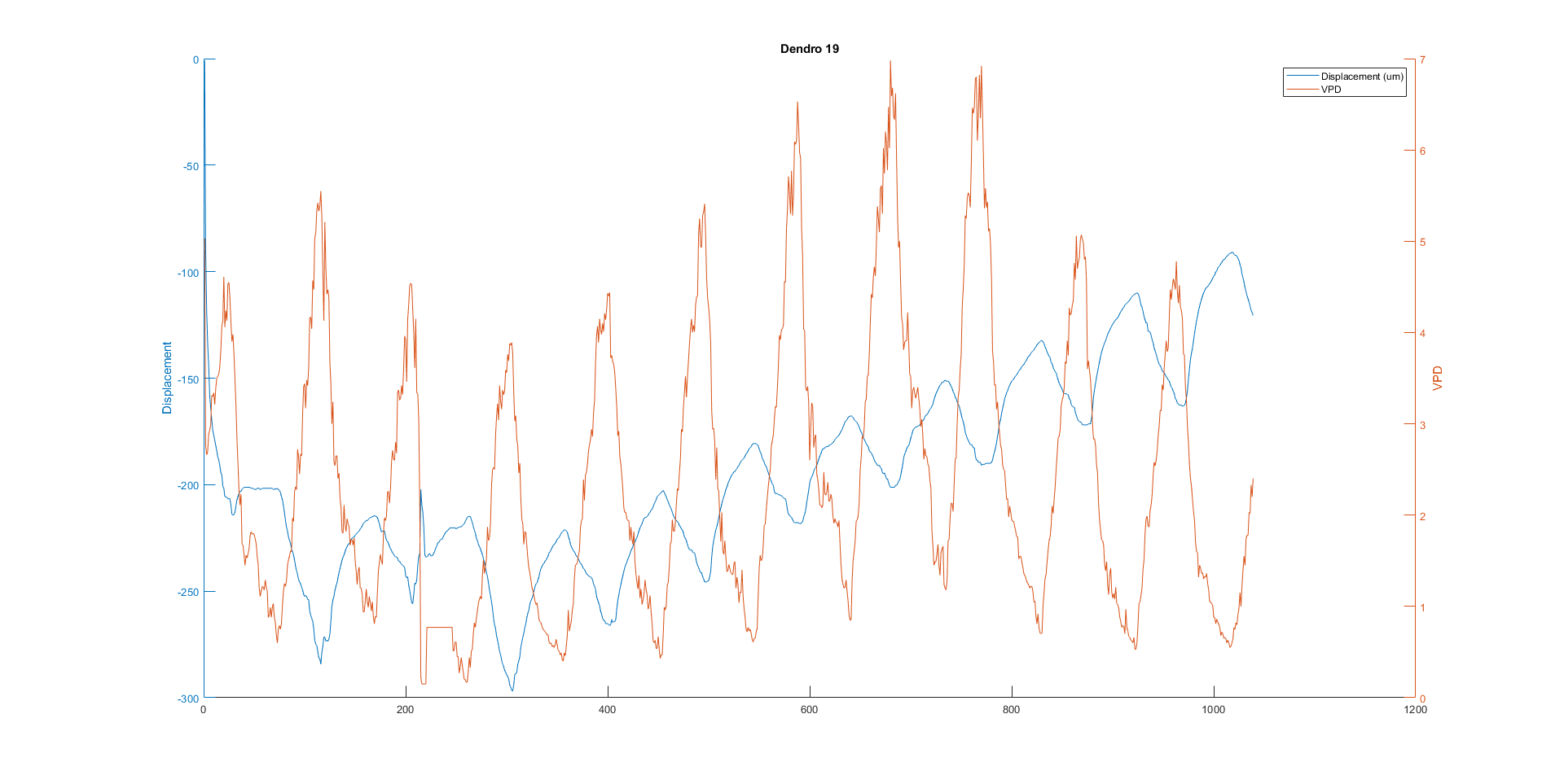
Author: Bryson Goto
Show More
Cameron and I went to the Southern Oregon Research and Extension Center (SOREC) to deploy 10 dendrometers in Dr. Levin's vineyard. These 10 have been tested for at least 2 weeks in the Lewis-Brown Farm for functionality. We will have another deployment in the next coming weeks for the last 10 dendrometers.
We split up the deployment into 2 parts so that 10 of the dendrometers can capture June data while the remaining 10 can be used to test functionality of new code additions in LB farms. Once the new additions are proven to work, the new code will be uploaded into the first 10 dendrometers so that all 20 will have the same code for the growing season.
Author: Bryson Goto
Show More
We got the results from the Lewis-Brown Farm deployment for some of the dendrometers as seen below. While most of the data was what we expected from our prototype, there were some graphs that had data that didn't seem accurate ranging from the displacement to temperature. For temperature, there were some outliers that we deduced was from direct sunlight over the sensor-- heating it up to a temperature not reflecting the environment. The inaccurate displacement data came from user errors such as magnet positioning during deployment to manufacturing errors. These errors are noted and will be marked down for future deployments and can be easily fixed.
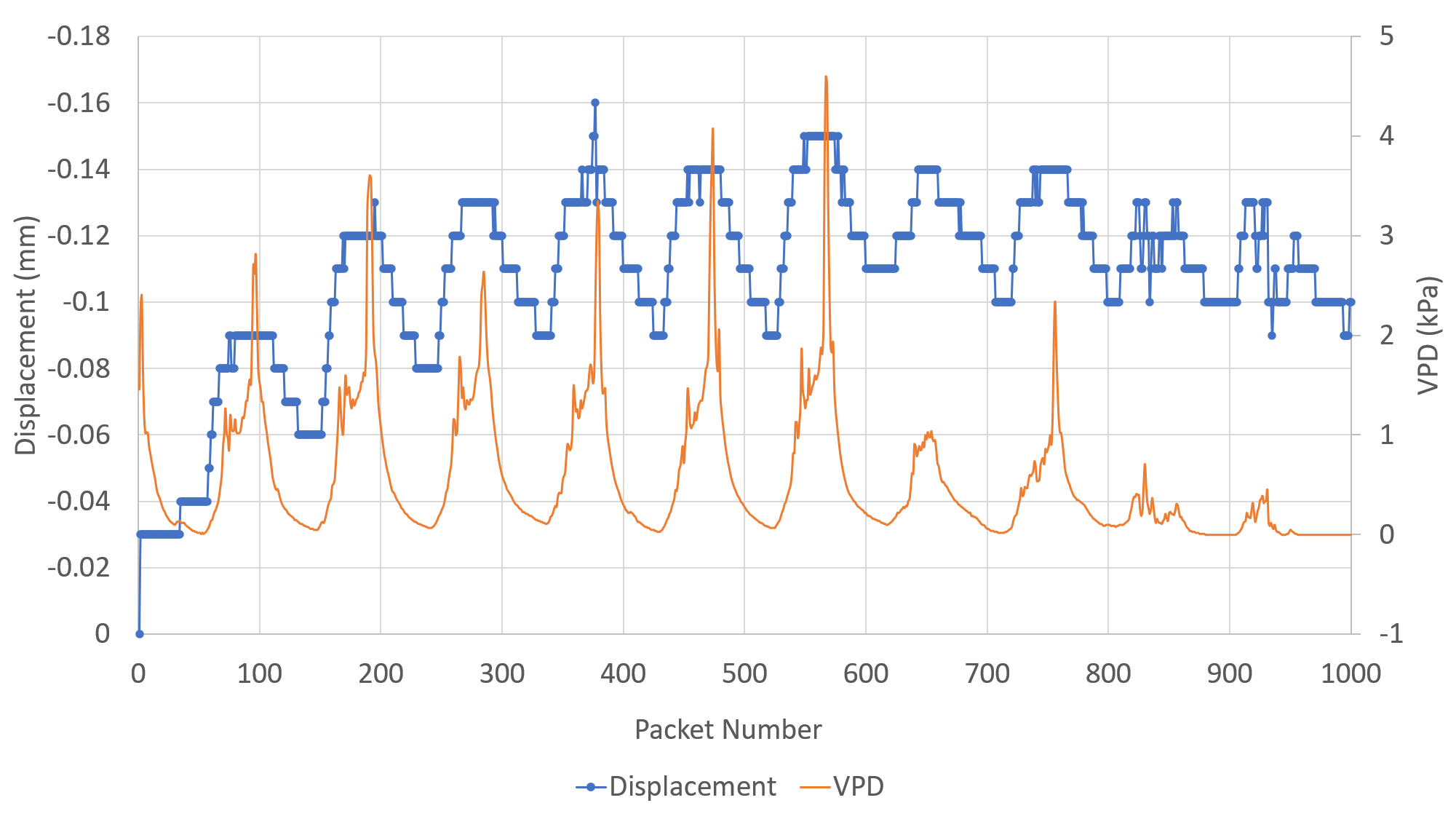
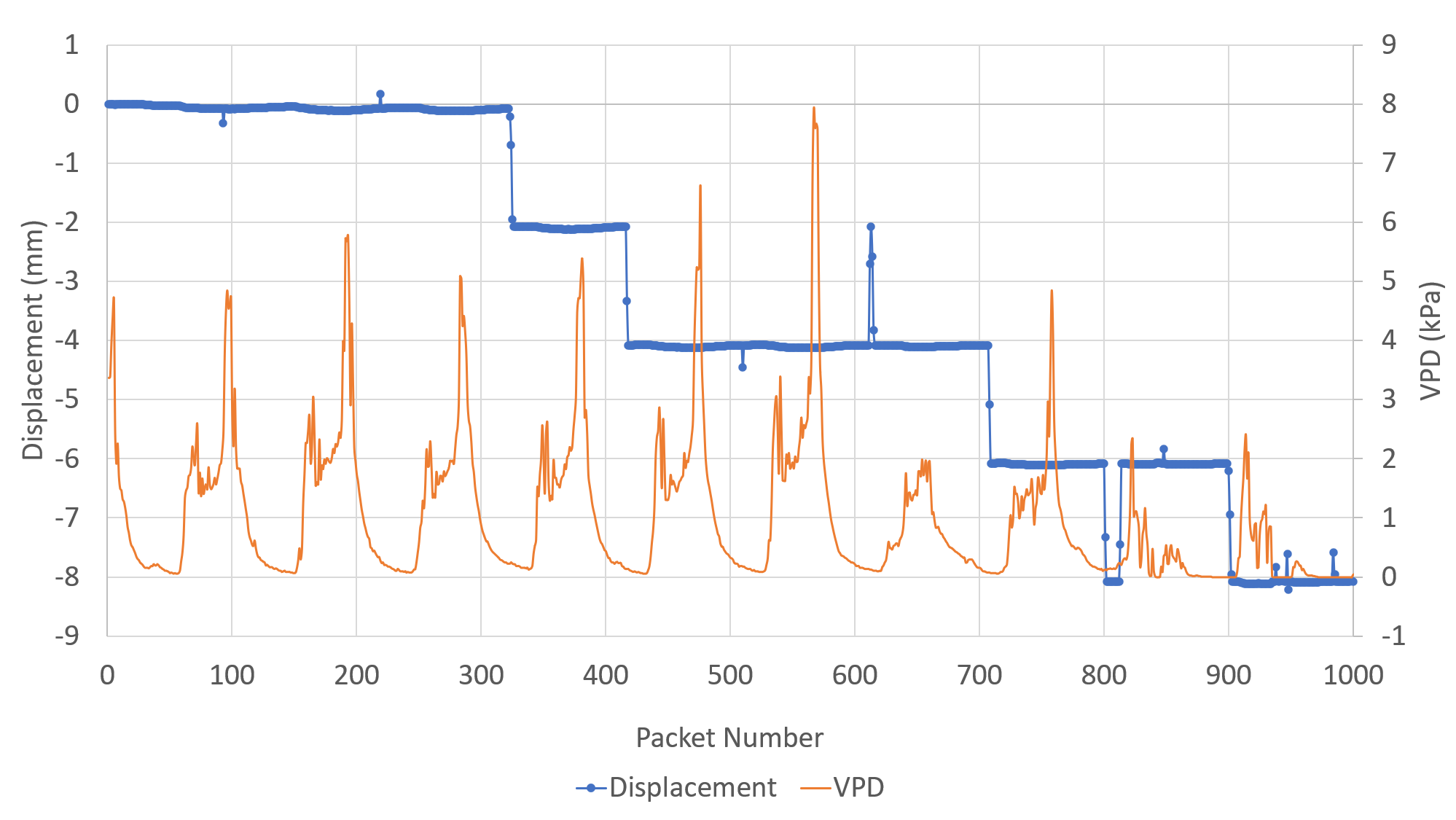
Author: Bryson Goto
Show More
Cameron and Logan (an OPEnS lab intern) deployed the currently made dendrometer prototypes at the Oregon State's Lewis-Brown Farm for initial testing before being deployed at Dr. Levin's vineyard. Changes were made during this time which include a different type of clamp for mounting the dendrometer as well as a LoRa antenna. However, the LoRa has not yet been configured to transfer at a reasonable range as of yet. All of the prototypes will be tested for functionality and durability for 2 weeks before deemed ready for deployment at Dr. Levin's vineyard.
The plants we used for testing were blueberries instead of grapevines, but it was still a good indicator whether the prototypes were functioning as expected.
Author: Cameron Clonch
Show More
We are officially transitioning to a waterjet cutter for dendrometer manufacturing. The design of the device has been modified such that the wishbone is one piece and the slider can move within slots on the wishbone. The frame has also been condensed to one continuous piece.
Author: Bryson Goto
Show More
The Dendrometer stakeholder, Alec Levin, was pleased with the progress that the Dendrometer project was making. After having a meeting with him as well as the lab director, it was decided that an order of 20 dendrometers would be made for the summer and fall growing season. The deadline for these orders would be end of May or mid June to capture the growing period of the crops. Efforts will be geared toward production and testing the system.
After the meeting, it was also discussed that telemetry is also desired via Long Range (LoRa) communication which would then upload to a Google Spreadsheet. In addition to production, progress toward telemetry will also be made aimed with a distance of 3-4 miles between the nodes and hub.
Author: Bryson Goto
Show More
The latest version of the Dendrometer was deployed on a camellia plant for 3 days (February 3-5). Despite being winter time, the dendrometer was deployed to verify the prototype's functionality with the upgraded changes from the October deployment (including pelican box, PCB design, LED indicator, and error bug tracking).
Displacement and temperature logged for each measurement
Displacement and Vapor Pressure Deficit (VPD) showing that despite temperature changing, displacement changes with respect to VPD
Results:
- Consistent tracking of daily stem diameter between 15-33µm
- Error tracking reported 0 bugs during the 3 days
Overall, the results were more successful than the last deployment in which there were 0 bugs that were found in this trial compared to the October trial. This means that no measurements were excluded due to system functionality issues and all of the movements were tracked and recorded. The stem fluctuations were smaller compared to the last trial due to the time of year as well as a different plant being tested. Through this trial, more features are being planned to increase the value of the prototype such as VPD calculations as well as LoRa communication.
Author: Cameron Clonch and Bryson Goto
Show More
The addition of an LED indication system is almost complete, save for a couple small issues with the code. We are continuing to work on documentation, including an instructional video, and building more prototypes. Plans for further testing on a Hydrangea plant in Corvallis, OR are set to commence in the couple weeks. Efforts are also being made to submit an open-source paper about this project to HardwareX very soon!
Author: Cameron Clonch, Mark Huynh, Bryson Goto
Show More
After performing multiday tests on a grapevine at Woodhall vineyards, we have gained several insights on current functionality of the system. The data continues to show that the dendrometer readings are largely independent of ambient temperature fluctuations and changes in grapevine diameter were recorded that match expected values. We are continuing to test the dendrometer on plants and on Pyrex cylinders to further identify necessary improvement and affirm that the data is truly temperature-independent.
For the mechanical design, we are in the process of evaluating the use of a waterjet cutter for producing dendrometer parts. If successful, the waterjet cutter could significantly reduce production time and improve accuracy in the machining process.
To improve the integration of the electronics and mechanical design, as well as to make the dendrometer more intuitive for user, we are working on incorporating an LED and push-button sensor check mechanism. Another thing that is currently being worked on is a custom PCB to connect all of the electronics. Having a custom PCB would remove the need to hand solder the wires and make it easy to connect / disconnect wires for assembling and disassembling the circuit.
Author: Cameron Clonch
Show More
The magnet and sensor are working well together and outputting accurate data when tested using a serial monitor in a controlled environment. Tests outside are being conducted on the branch of an apple tree to evaluate and refine the SD output and generate further considerations for the user interface/experience in all aspects of system design.
We have adjusted the mechanism for securing the dendrometer to the vine so that the only point of contact for the piece responsible for moving the magnet (the T-shaped part) is at the back of the vine. This will maintain that motion is only being created by one point on the vine, reducing measurement uncertainty that could otherwise be produced by something that squeezes/touches the vine at multiple points. This change also makes installation easier - the piece securing the magnet (and its mount) to the back of the vine slides onto the rods (sandwiching them), then two nuts are used to tighten the apparatus together and against the vine.
We are currently working on adding a feature that provides indication of proper setup so that all parameter requirements for the AS5311 sensor are maintained. We will also continue to perform outdoor tests and work to refine the design so that it is more user friendly and the product/process is easy to repeatedly duplicate.
24 hour test of the dendrometer in an apple tree outside
Author: Cameron Clonch
Show More
A mechanical design is currently being tested, and small adjustments are being made in the process. The design utilizes zero-thermal expansion carbon fiber, mitigating inaccuracies from material behaviors. It also relies on spring tension to create and track movements from diurnal changes in the grapevine. Using a spring-based design prevents friction or other barriers from impeding on the motion created by the diurnal fluctuations.
The design is being refined based on observations and considerations for system installation/deployment (how easy it is to put on a grapevine and start getting data), stability, electrical compatibility, ease of maintenance and data collection, and improving measurement accuracy by evaluating the dendrometer's interaction with the vine/vine growth.
We are also in the process of integrating the electronics prototype with the mechanical design, as well as testing their combined functionality.
Goals:
- Ensure the magnet is moving linearly and level with the AS5311 sensor, retaining the distance between the top surface of the magnet and the sensor
- Successfully record data from the electronics prototype when connected to the mechanical structure
- Run tests on a grapevine for several days to see if data is collected and evaluate the accuracy of the data output
- Improve installation process by installing the device on several vines and adjusting design to accommodate common issues/concerns, then create a thorough implementation guide to accompany the design for field testing
- Fix issues with the code/electronics erroneously outputting random numbers
- Provide enclosure for protecting the dendrometer from weather, animals, etc. in the field
Author: Mark Huynh
- Obtained magnets for testing and currently prototyping possible structures
Show More
A mechanical engineer has been hired onto the team and is working on possible mechanical systems to attach the sensor to a grapevine on the field. Various designs are currently in discussion, including a possible clamp-style Dendrometer, while also taking into consideration past designs as well.
Having recently obtained new 2mm pole length magnets, our team can start planning for tests to verify the resolution of the sensor. We are currently in the process of obtaining a micrometer tool in order to ensure that the outputted readings of the sensor are accurate under various conditions such as temperature.
Show More
The Hypnos Board was added to this project, which incorporates SD card and RTC functionality. In addition to this, Loom software was integrated, allowing old code to be remove and have the functionality offloaded to this library. In the future, this will potentially allow for the use of Sleep mode which allows for less power consumption once deployed.
For this upcoming Spring, a mechanical specialist will be on-boarded for this project and will focus on the mechanics of the system. In the meantime, we are trying to get a hold of a viable magnet supplier in order to be able to perform future tests with various magnet shapes and sizes.
Temperature Dependency
The new sensor that this design is integrating is an extremely high-resolution magnetic linear sensor, the AS5311. According to its data sheet, along with rough in lab testing, this linear sensor is able to precisely measure linear movement with a resolution of up to ~488nm. Contrast this to the previous design, which utilized a 3048L linear potentiometer and had a precision of ~12.5 microns.
Additionally, tests have indicated that the previous design had a serious temperature dependency that resulted in inaccurate readings that prevent it from being deploy-able. In response to that, lab tests were conducted with the new sensor with temperatures ranging up to 42 degrees Celsius. The results demonstrate that this magnetic sensor has an error of ~.002% within this temperature range. As can be seen in the chart below, with fluctuating temperatures and humidity, the magnetic sensor is able to output a consistent value.
Contrast that to tests performed with the previous potentiometer design, where a slight fluctuation in temperature made a significant impact on the data outputted. Furthermore, the AS5311 magnetic sensor is less than half the price of the previous potentiometer.
Data from Version 1 Potentiometer Design. Temperature caused the displacement measurements to vary substantially.
Measurement Accuracy
The AS5311 sensor was tested for accuracy using digital calipers with 10 micron precision to move and track the motion of the magnet. The values produced by the calipers and the linear sensor were compared to ensure that the sensor was accurately recording the changing movements of the magnet.
Show More
After determining that the previous potentiometer design was too temperature dependent, a magnetic linear encoder was introduced as a possible solution.
This sensor is the AS5311 and its data sheet indicates a resolution of up to ~488nm, which was much more accurate than the previous linear potentiometer. In order to confirm that this sensor is not temperature variant like the previous design, tests were run with this sensor in a controlled oven.
(Todo: Insert graph here)
This test was conducted with the sensor outputting serial data with a stationary magnet on top of it. Ideally, the serial output of the AS5311 should remain constant (within a range of 0-4096) which signifies that the sensor is correctly determining the magnet on top of it is not moving.
As can be seen by the graph, with large fluctuations in temperature the sensor is able to accurately depict that the magnet on top of it is stationary.
For convenience with testing and deployment, the data that is outputted by the sensor can be logged onto a Google Sheet. This was done through interacting with Google's Google Sheet API.
While a mechanical specialist focuses on incorporating the new sensor onto the single point attachment style for future testing, the software will slowly migrate to become integrated with Loom. Capabilities such as SD writing, temperature sensing, and possibly Google Sheet logging will become offloaded onto the Loom platform to allow robustness and will help will power efficiency in the future of this project.
Mark Huynh
Show More
We are moving away from the previous design to a single point attachment style.
The old design:
The first iteration of the single point style:
Drawing can be found here.
There are a few reasons behind this decision.
-
The collar design was unstable at small grape trunk diameters (<20 mm). It was unclear if even at larger diameters (20-40 mm) the collar design would have been able to withstand the usual weather and and debris from being outside in the field.
-
Moving to the single point attachment style reduces the number of components that could affect the measurement due to thermal expansion.
-
The single point attachment style greatly simplifies the design.
The new design is loosely based off of this design by Phytech which is designed for almond orchards. The above model is designed for the small grape trunk diameter, as well as the linear motion potentiometer.
In October we discovered we were having some significant problems with temperature sensitivity.
For the last month we have been doing tests on other possible linear motion potentiometers. To start, we have been testing the P3 LMC8, P3 LMC8R (same as first sensor listed but with a spring return), and Sensata 9610.
** Gabie Griffin **
- Project Planning
- Prototyping
- Synthesis
- Lab Testing
- Field Testing
- Finalization/Production
- Poster/Presentation
- Publication
- CRES
- Dendrometer
- Djinn
- eDNA Sampler
- eGreenhouse
- Evaporometer
- FloDar
- HyperRail
- Hypnos
- Isotopic Sampler
- Lilypad
- Loom
- Micro-Aggregating Sewer Sampler
- Mooraca
- OPEnSampler
- Pied Piper
- Rag Guard
- Rain Gauge Calibrator
- RainSavor
- RFID Moisture
- Sap Flow Meter
- SitkaNet
- Slide Sentinel
- Smart Rock
- Spool
- WeatherChimes
- Weed Warden
- Wisp
- Archived Project Blogs